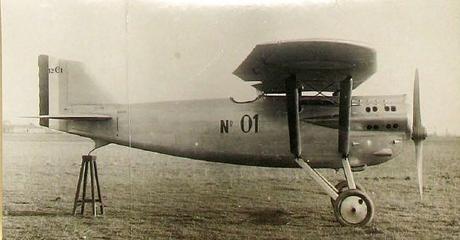
Le site historique de Saint Eloi est situé au cœur de la ville rose dans le quartier des Minimes et occupe une superficie de 65 000 m² à laquelle s'est ajouté en 2016 un deuxième site à proximité des pistes de l'aéroport de Blagnac. Ces deux sites représentent aujourd'hui une superficie totale de 75 000 m².
Le site de Saint Eloi est le premier centre d'expertise européen aéronautique de transformation des métaux durs, notamment le titane. Il est aussi spécialisé dans le développement, la fabrication, l'assemblage, l'équipement et les essais des mâts réacteurs des avions Airbus de la famille A320 jusqu'à l'A350, ainsi que le développement et la production de pièces de nacelles en titane (support et capot du moteur) .
Le mât réacteur (photo) est la pièce maîtresse fixée à la voilure qui soutient le moteur, et transmet les charges et la puissance des réacteurs à l'avion. Il est extrêmement sollicité par les vibrations aérodynamiques. Il abrite tous les circuits qui alimentent le moteur. Cet élément essentiel doit être léger et résistant à des températures allant de -50° à +600°C. Il est principalement fabriqué en titane.
Une fois assemblés et testés, tous les mâts réacteurs sont acheminés vers les chaînes d'assemblage final des avions Airbus de Toulouse, Hambourg (Allemagne), Mobile (USA) et Tianjin (Chine) pour y être fixés aux voilures des avions.
En 2021, l'usine Saint-Eloi est le seul site dans le monde à concevoir, usiner, produire, assembler et livrer les mâts réacteurs pour les avions Airbus. Les métiers artisanaux comme la chaudronnerie et le formage de pièces y côtoient les métiers d'ingénierie.
Près de 27 000 mâts réacteurs ont été produits à Saint Eloi depuis mai 1969, date du lancement de l'A300, le tout premier programme avion d' Airbus.
Le site de Saint Eloi compte aujourd'hui près de 1 000 collaborateurs.
1921- 1945: L'ère Dewoitine
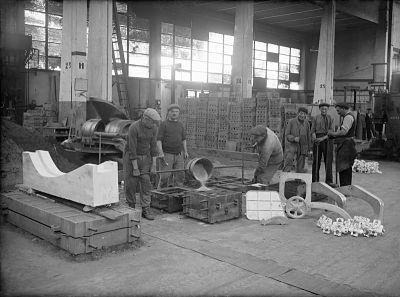
En 1921, de nombreux constructeurs, motoristes, acteurs industriels sont déjà présents à Toulouse, comme la Société des Ateliers d'Aviation Louis Breguet depuis 1910, et la Société Générale d'Entreprises Aéronautiques depuis 1917 avec Latécoère - qui embauche Emile Dewoitine comme chef de fabrication. Il démissionnera en 1921 pour créer sa propre entreprise. Loin de Paris et hors de portée (théorique) des bombardements, Toulouse avait l'avantage d'abriter des ouvriers chaudronniers et des ouvrières "tendeuses de toiles". Ils ont contribué à la fabrication des premiers avions à ailes souples, comme le planeur P1, puis à la mise au point de la voilure à mono longeron métallique (Photo), rendant la structure rigide ; une innovation d'Emile Dewoitine qui va révolutionner la construction aéronautique.
Emile Dewoitine crée la société CAED (Constructions Aéronautiques Emile Dewoitine) à Toulouse et loue le 20 mai 1921 un ancien entrepôt de salaisons de 4 000m2 dans le quartier " Pasteur " attenant à l'usine Saint Eloi actuelle. Rapidement, il met au point un chasseur monoplace, le D1(Photo). Cet avion effectue son premier vol en novembre 1922 et sera un premier succès car produit à 234 exemplaires.
En juillet 1934, il aménage un bâtiment de plus de 6 000 m2. Plus de 400 appareils sont produits dans cette usine nommée Saint Eloi.
Fin 1938, les cadences de fabrication continuent d'augmenter. La guerre menaçant, le gouvernement français regroupe et nationalise les usines toulousaines sous le nom de Société Nationale de Constructions Aéronautiques du Midi (SNCAM). Emile Dewoitine, aux commandes de cette société, décide alors de bâtir un premier hall d'assemblage sur le lieu- dit Saint Martin du Touch, et d'agrandir le site Saint Eloi, le portant à 28 000 m2. Toulouse devient alors la Capitale de l'Aéronautique : près de 10 000 personnes y produisent une centaine d'avions par mois !
L'armistice de 1940 met un coup d'arrêt brutal à cette aventure et oblige l'usine Saint Eloi à effectuer une reconversion temporaire. Pendant cinq ans, les moyens industriels de St Eloi et les métiers de la chaudronnerie et de formage (photo) sont parfaitement adaptés à la fabrication de petites séries telles que la fabrication de bicyclettes à cadre embouti en alliage léger, des fours auto-carbonisateurs capables de produire du charbon de bois, des remorques à gazogène pour automobiles et camions (Photo), des parties arrière de carrosseries d'autocars (Photo), des conteneurs métalliques pour des camions (Photo) et le chemin de fer, et des meubles métalliques de bureau et de cuisine.
1945 - 1970 : Début de l'ère industrielle. De l'artisanat à la haute technologie.
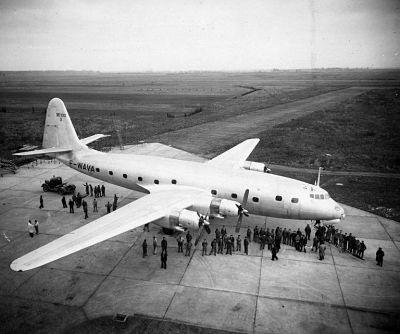
C'est la reprise avec les années d'après- guerre ! La formation est un facteur majeur de cette reprise. D'une activité artisanale, Saint Eloi passe à un mode industriel.
Sur cette période, les équipes de Saint Eloi participent déjà aux premiers grands programmes d'avions civils comme "le Languedoc", "l'Armagnac"(photo) et le "Concorde (photo)".
Pour y parvenir, l'usine a recours à l'apprentissage.
En 1949, Saint Eloi accueille une école capable de former 40 élèves par an et de les préparer aux BEP et CAP de chaudronnier (photo), usineur, fraiseur et ajusteur. Aujourd'hui, le Lycée Airbus (photo) est l'un des rares lycées d'entreprise en France qui offre à près de 300 élèves des formations à cinq Bac Pro, deux BTS et une mention complémentaire Peinture.
L'expertise du personnel est aussi reconnue dans le cadre du concours "Meilleur Ouvrier de France". Depuis 1980, ce sont plus de 44 salariés Airbus qui ont gagné ce concours dans des catégories comme la dinanderie d'art ou la maquette industrielle.
Le développement du premier avion Airbus est lancé officiellement au Salon aéronautique du Bourget, en 1969 : il s'agit de l'A300B (Photo) . Les deux partenaires sont Aérospatiale, côté français, et Deutsche Aerospace, côté allemand.
Les pièces élémentaires du mât réacteur de cet avion (photo) sont alors usinées à Saint Eloi puis assemblées à Blagnac.
1970 à 1990 : Démarrage de l'ère Airbus
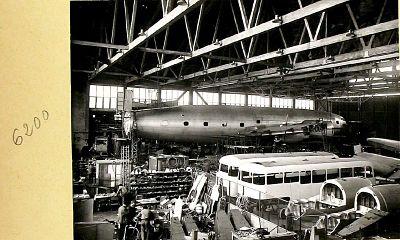
Pour faire face à la concurrence américaine dans une situation de marché très concurrentielle, le GIE Airbus Industrie, Groupement d'Intérêt Économique, est officiellement créé en décembre 1970 . Il formalise la coopération entre les différents partenaires français, allemand, britannique et plus tard espagnols et propose aux clients d' Airbus une interface unique pour la vente, la commercialisation et le support aux clients.
Fin 1975, Airbus détient déjà 10% du marché mondial des avions civils et affiche un total de 55 avions dans son carnet de commandes.
Au début des années 80, des pièces de haute technicité sont usinées par des experts en chaudronnerie et tôlerie. On parle de "cousu main". Saint Eloi prépare aussi sa transformation technologique et intègre de nouvelles machines ultra performantes.
Trois unités sont alors créées au sein de l'usine : le Traitement de surface, la Tôlerie qui accueille des étireuses de matière première très encombrantes, et une machine-outil équipée de portiques à trois têtes pour usiner des pièces très complexes. Le bâtiment dit Bobillot (situé en face de Saint Eloi) intègre la CFAO (Conception et Fabrication Assistées par Ordinateur) qui mettra fin à la fabrication manuelle de maquettes.
Fin des années 80, quatre programmes d'avions sont alors au catalogue d' Airbus : l'A300B (depuis 1969), l'A320 (depuis 1984) et les A340/A330 (depuis 1987).
Les équipes d'ingénieurs du Bureau d'Etudes d' Airbus viennent alors s'installer sur le site de production de Saint Eloi pour concevoir et mettre à jour les produits, au plus près des ateliers.
En 1987, les activités d'assemblage des mâts réacteurs des A320 sont transférées du site de Blagnac vers le site Saint Eloi.
Plusieurs idées innovantes vont transformer l'usine :
- L'abandon des grilles de perçage et l'investissement dans les machines à commande numérique et laser 3D.
- L'acheminement des mâts réacteurs vers la presse : utilisation novatrice d'un chariot équipé du système filoguidé avec la création d'un marbre pour conserver la référence de la position du mât avant son usinage.
- La mise en place d'outillages modulaires qui permet de produire différents produits : 80% de similarité entre tous les programmes d'avions Airbus .
L'Usine Nouvelle (magazine français consacré à l'économie et aux technologies dans le monde industriel) attribue en 1990/1991 le Grand Prix de la Production à Saint Eloi. Ce même prix sera décerné une nouvelle fois à Saint Eloi en 2011 pour l'organisation "Lean" de sa production.
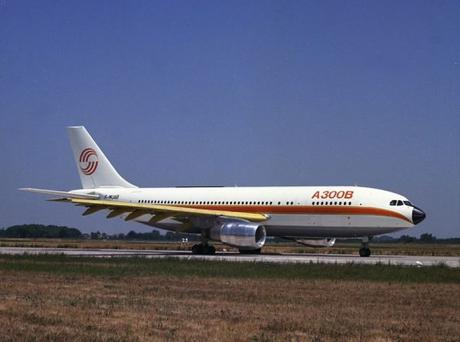
De 1990 à 2011 : Performance Industrielle
Saint Eloi est reconnue pour ses métiers et compétences, et pour sa performance. Les cadences de production des Airbus augmentent et le site de Saint Eloi s'agrandit.
A fin 1990, plus de 450 mâts réacteurs sont livrés chaque année. Une entreprise attenante à Saint Eloi est rachetée et la rue de la Manutention, qui sépare deux bâtiments Airbus est intégrée au site. Saint Eloi investit en intégrant des machines-outils innovantes comme des tours numériques d'un fournisseur japonais, un SPF (Super Plastic Forming) et une machine de perçage de mâts de la société Jobs, le "must" à cette époque.
Quelques années plus tard, Saint Eloi livre près de 800 mâts réacteurs par an. Il faut encore s'agrandir et s'adapter à l'augmentation des cadences des programmes A320, A330, A340 d' Airbus et des turbopropulseurs d'ATR.
Les équipes du Bureau d'Études planchent sur les bâtis moteurs de l'A400M et de l'A380. Le site s'engage dans une démarche environnementale et de sécurité des postes de travail encore plus importante. La décision est prise d'externaliser toutes les activités liées aux traitements de surface des pièces produites.
En 2010 : création d'un tout nouveau hall dédié à l'assemblage des mâts-réacteurs de l'A350 représentant un investissement de 15,5 millions d'euros. Ce nouveau hall abrite la toute nouvelle "flowline", un système permettant le passage des pièces d'un poste de travail à un autre grâce à un pont roulant.
2011 à 2021 : Centre d'expertise et d'excellence
Pour s'adapter aux nouveaux produits et aux évolutions des cadences de production, les équipes font face à des modifications industrielles majeures.
L'usine de Saint Eloi évolue aussi pour répondre aux nouveaux développements (familles NEO, motorisations CFM, P&W...).
C'est une entreprise modèle pour beaucoup d'autres entreprises qui viennent régulièrement visiter le site. C'est aussi l'esprit "familial" qui en fait sa renommée.
Pour la première fois, en 2011, une femme, est nommée à la tête du site industriel d' Airbus.
En 2016, face à la croissance des activités et l'augmentation des cadences de production des mono-couloirs, un deuxième site vient compléter l'usine de Saint Eloi à proximité des pistes de l'aéroport de Blagnac.
Saint Eloi est une usine qui regroupe de nombreuses compétences, non seulement techniques mais aussi en organisation industrielle. L'expertise des équipes sur le travail des métaux durs, du titane et des alliages n'est plus à démontrer. L'innovation sur l'organisation des ateliers et du système industriel a aussi permis d'amener l'usine vers l'excellence.
Saint Eloi maîtrise le processus global de production des mâts réacteurs, élément d'une très haute technicité, depuis le premier copeau de métal jusqu'à la livraison du mât réacteur.
L'usine a souvent été choisie comme site pilote pour tester de nouveaux outils et de nouvelles solutions.
Le futur
La transformation d' Airbus est en marche, avec l'ambition de se préparer à développer et produire d'ici une dizaine d'années le prochain modèle de monocouloir, avec comme défi principal la réduction des émissions de CO2.
C'est dans ce contexte que Saint Eloi développe sa stratégie industrielle. Centre d'Expertise pour les métaux durs, Saint Eloi demeure le "fournisseur" principal d' Airbus pour les mâts réacteurs de nouvelle génération, permettant d'accueillir des motorisations plus économes en carburant et en émissions de CO2, voire totalement décarbonées grâce à l'hydrogène.
L'ambition de Saint Eloi est également de fabriquer un élément propulsif complet et intégré, de produire des pièces élémentaires stratégiques, complexes et à forte valeur ajoutée, et de rester la référence sur le travail des métaux durs, pour l'ensemble propulsif comme pour d'autres pièces de structures complexes.
Source : Airbus